Expert Houston Welding Inspection: Guaranteeing Structural Integrity and Safety
Expert Houston Welding Inspection: Guaranteeing Structural Integrity and Safety
Blog Article
Checking Out the Fundamentals of Welding Inspection: A Detailed Evaluation of Procedures, Tools, and the Significance of Quality Assurance in Welding Industries
Welding inspection offers as a foundation in the maintenance of security and architectural stability across various industries. Understanding the ramifications of these practices elevates vital inquiries concerning their effectiveness and the future direction of quality assurance in welding.
Importance of Welding Evaluation
Welding inspection plays a crucial role in guaranteeing the integrity and safety and security of bonded frameworks. It offers as an organized approach to examining weld quality, identifying potential defects, and guaranteeing compliance with established standards and specifications. The importance of welding examination extends past plain adherence to guidelines; it is critical in securing human lives and securing financial investments in infrastructure.
Faulty welds can bring about disastrous failures, causing significant economic losses, injury, or loss of life. As a result, extensive assessment procedures are important to find issues such as insufficient infiltration, porosity, or splits prior to they rise into essential failures. Furthermore, effective welding inspection contributes to the total performance and long life of structures, making sure that they can withstand the problems for which they were developed.
Moreover, the execution of welding assessment cultivates a culture of high quality and accountability within the welding market. By prioritizing inspection, companies show their commitment to quality, consequently improving their credibility and competitiveness in the market. Inevitably, welding inspection is not simply a procedural action yet a basic component of engineering stability and security assurance, crucial for the effective implementation of welding jobs throughout numerous fields.
Trick Inspection Processes
A thorough strategy to welding examination includes several key procedures that are necessary for making sure weld high quality and structural honesty. The very first crucial procedure is aesthetic examination, which permits examiners to identify surface area defects such as splits, porosity, and incorrect grain appearance. This method functions as a preliminary analysis to make sure that the weld satisfies specified criteria.
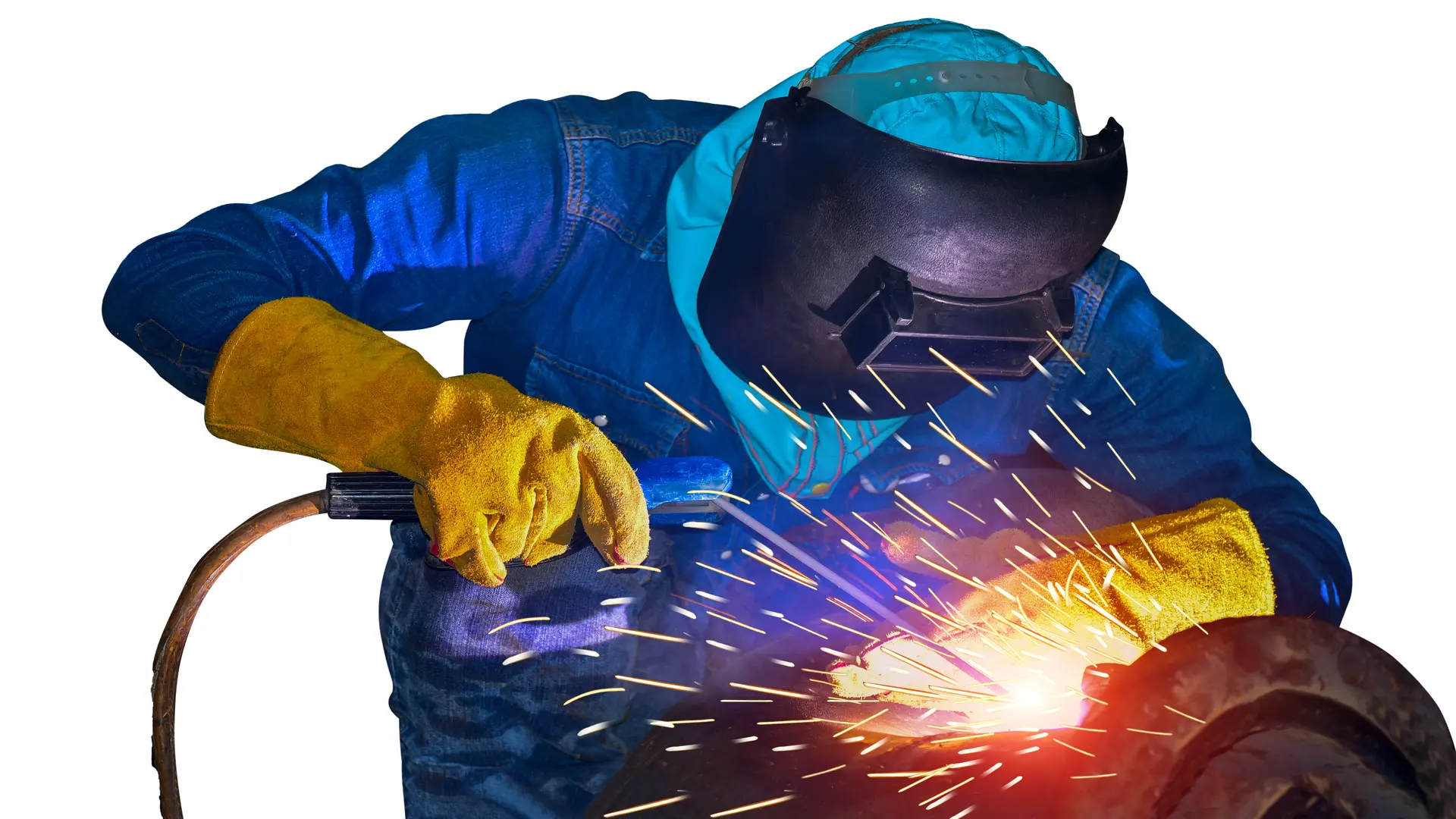
Furthermore, harmful screening might be executed on sample welds to analyze their mechanical residential or commercial properties and performance under anxiety. This procedure includes tiredness, tensile, and influence testing to validate that the weld can endure operational conditions.
Finally, paperwork and reporting are crucial components of the examination procedure. Preserving precise records of inspections, monitorings, and examination results helps ensure conformity with sector requirements and helps with continuous improvement in welding techniques. Collectively, these key procedures develop the backbone of reliable welding evaluation and quality control.
Tools for Weld Evaluation
Countless devices are essential for reliable weld assessment, each designed to examine different aspects of weld quality and performance. Amongst the most commonly used are aesthetic examination devices, consisting of magnifying glasses and borescopes, which allow assessors to determine surface area defects such as fractures, porosity, and improper blend.
Furthermore, ultrasonic screening (UT) equipment is important for spotting inner flaws. This device employs high-frequency audio waves to disclose interruptions within the weld, ensuring the stability of the product. Radiographic testing (RT) tools, which make use of reference X-rays or gamma rays, similarly offer understanding right into the inner structure of welds, permitting for the recognition of additions or gaps.
For precise measurements, calipers and assesses play a significant role in ensuring and determining weld dimensions adherence to defined resistances. Solidity testers review the mechanical buildings of the weld, guaranteeing it meets efficiency standards.
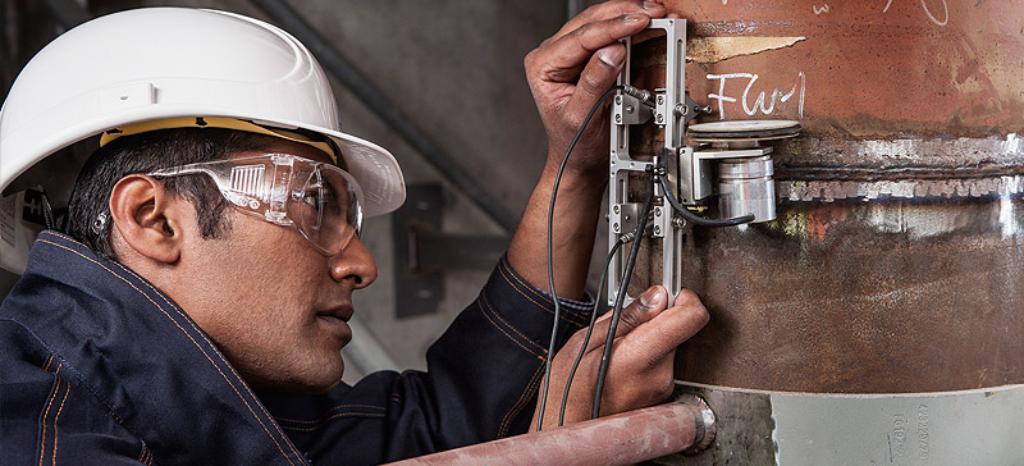
Strategies for Evaluating Quality
Just how can the top quality of welds be reliably examined? A selection of methods are used to evaluate weld integrity and make sure adherence to defined standards.
Ultrasonic testing (UT) is another famous strategy that uses high-frequency sound waves to find inner imperfections within the weld. Houston Welding Inspection. This method offers an extensive sight of the weld's integrity without endangering its architectural honesty. In addition, radiographic testing (RT) his explanation uses X-rays or gamma rays to expose internal problems, offering thorough understandings into weld top quality
Magnetic fragment screening (MT) is effective for discovering surface and near-surface stoppages in ferromagnetic materials, utilizing electromagnetic fields and tinted fragments to highlight issues. Dye penetrant screening (PT) can be used to uncover surface-breaking problems by applying a dye that permeates right into splits and is ultimately exposed.
Compliance With Sector Requirements
Compliance with market requirements is important for making sure the quality and safety and security of bonded structures. These criteria, developed by companies such as the American Welding Society (AWS) and the American National Requirement Institute (ANSI), supply guidelines that control the welding process, products, and examination procedures. Following these requirements not only makes sure the structural stability of welds yet likewise reduces threats related to failings that could cause catastrophic effects.

Welding examiners are entrusted with validating compliance with these requirements throughout the welding process (Houston Welding Inspection). This involves examining welding treatments, monitoring welder certifications, and performing comprehensive examinations of the final item. Non-compliance can cause significant monetary consequences, task hold-ups, and damages to a firm's credibility
Normal training and updates on criteria are vital to keep personnel informed and skilled, making certain that all facets of Resources welding operations meet or go beyond regulative requirements. Ultimately, dedication to market standards offers as a foundation for excellence in the welding industry, advertising security and reliability in bonded structures.
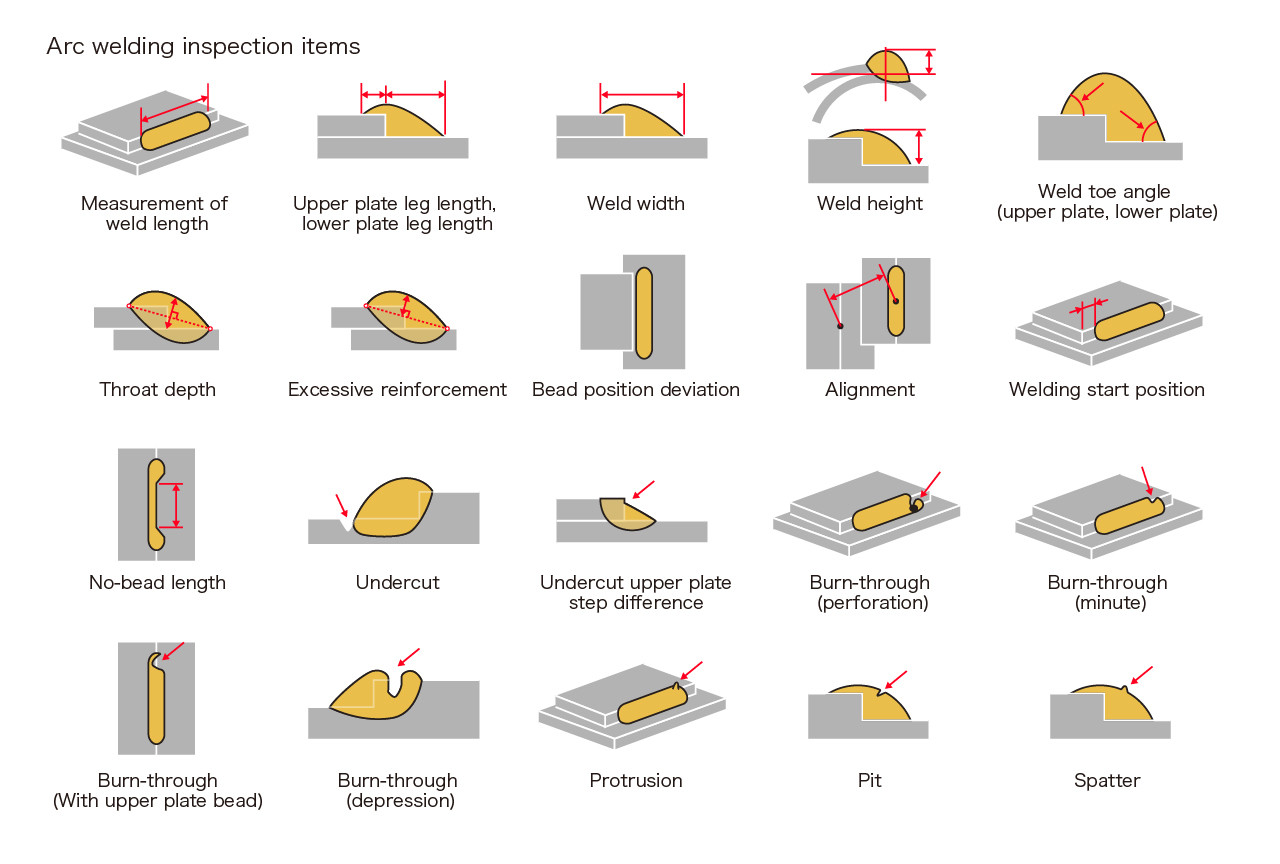
Conclusion
In final thought, welding assessment offers as a critical element in preserving the security and stability of welded structures. Adherence to industry standards ensures compliance and advertises a culture of quality within the welding industry.
Moreover, the execution of welding examination cultivates a society of high quality and responsibility within the welding market. Eventually, welding inspection is not merely a step-by-step action however a fundamental part of design honesty and security guarantee, important for the successful implementation of welding jobs across numerous markets.
A comprehensive approach to welding assessment includes numerous key procedures that are essential for ensuring weld top quality and structural integrity. These standards, developed by organizations such as the American Welding Culture (AWS) and the American National Criteria Institute (ANSI), offer guidelines that control the welding process, products, and evaluation methods.Welding examiners are entrusted with confirming conformity with these requirements throughout the welding process.
Report this page