Houston Welding Inspection: Accuracy Testing for Optimum Structural Health And Wellness
Houston Welding Inspection: Accuracy Testing for Optimum Structural Health And Wellness
Blog Article
A Comprehensive Overview to Recognizing How Welding Evaluation Functions: Strategies, Standards, and Best Practices for High Quality Guarantee in Steel Manufacture
Understanding the complexities of welding assessment is critical for maintaining the stability of metal construction. Various techniques, such as ultrasonic and visual testing, play a critical function in determining possible flaws, while adherence to developed standards ensures compliance and durability. Applying finest practices can significantly improve high quality assurance steps. However, the landscape of welding evaluation is not without its challenges. What difficulties develop in the area, and exactly how can these be successfully alleviated? Checking out these aspects reveals the deepness of this necessary self-control.
Significance of Welding Inspection
Although welding is a critical procedure in various sectors, its stability straight affects the safety and security and performance of structures and elements. Effective welding assessment is important for recognizing problems that can compromise the top quality and resilience of bonded joints. This process makes sure adherence to established requirements and requirements, which are important for keeping structural integrity and operational dependability.
Welding inspection serves numerous purposes, consisting of verifying that the welding procedure has been carried out appropriately, assessing the high quality of products made use of, and confirming that the finished product fulfills regulatory and market standards (Houston Welding Inspection). Through rigorous assessment, possible concerns such as porosity, cracks, and incomplete combination can be found early, preventing costly repair services and minimizing security threats
Moreover, consistent welding evaluations foster confidence among stakeholders, including engineers, clients, and regulatory bodies, by demonstrating a commitment to quality assurance. The relevance of welding inspection can not be overstated; it is essential not only for conformity with legal demands however also for enhancing the general efficiency of welded structures. Inevitably, a robust welding inspection program is a proactive procedure that safeguards against failings, guaranteeing the longevity and reliability of bonded parts in their intended applications.
Typical Welding Assessment Techniques
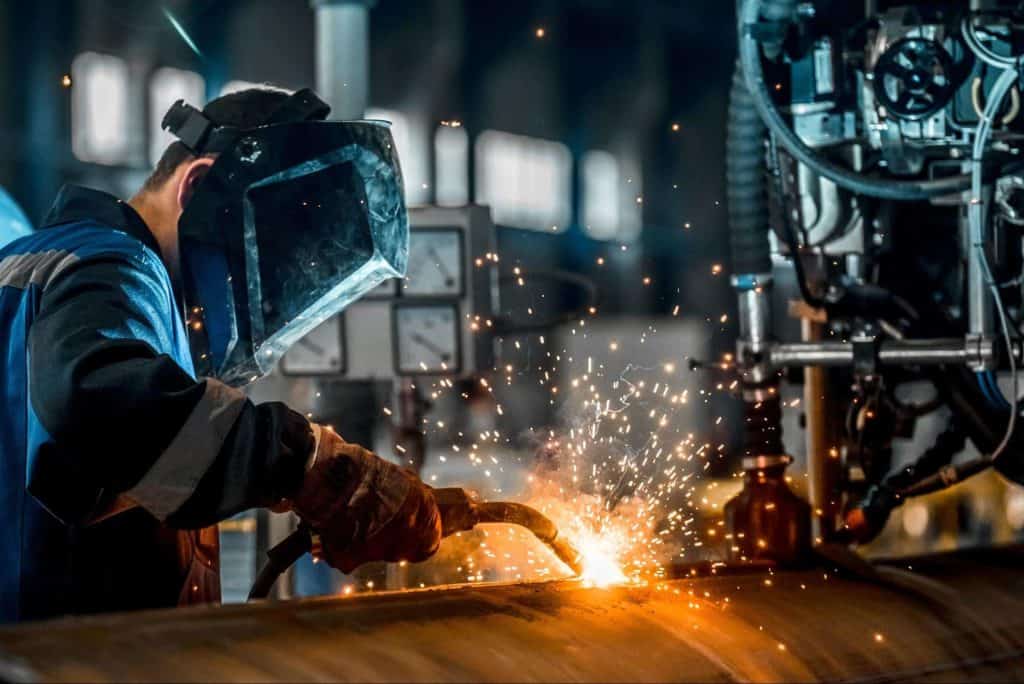
Aesthetic evaluation is the very first line of defense, enabling examiners to determine surface flaws such as fractures, damages, or incomplete blend. Radiographic testing uses X-rays or gamma rays to reveal interior defects, making it ideal for intricate welds. Ultrasonic testing employs high-frequency sound waves to detect subsurface problems, providing accurate dimensions of weld integrity.
Magnetic bit screening works for ferromagnetic materials, highlighting surface and near-surface suspensions when particles are related to a magnetic field. Conversely, color penetrant testing uses a liquid color to disclose surface-breaking flaws, guaranteeing that also the smallest imperfections are found.
Each strategy has its strengths and restrictions, often requiring a combination of techniques for thorough analysis - Houston Welding Inspection. By applying these inspection techniques, high quality assurance in metal construction is accomplished, making certain that bonded frameworks meet security and efficiency standards
Market Requirements for Welding

The American Welding Society (AWS) and the American National Standards Institute (ANSI) are 2 famous organizations that develop welding requirements. AWS D1.1, as an example, describes the requirements for welding steel frameworks, while AWS D1.2 concentrates on aluminum. Internationally, the ISO 3834 standard addresses top quality needs for combination welding, providing a structure appropriate across nationwide borders.
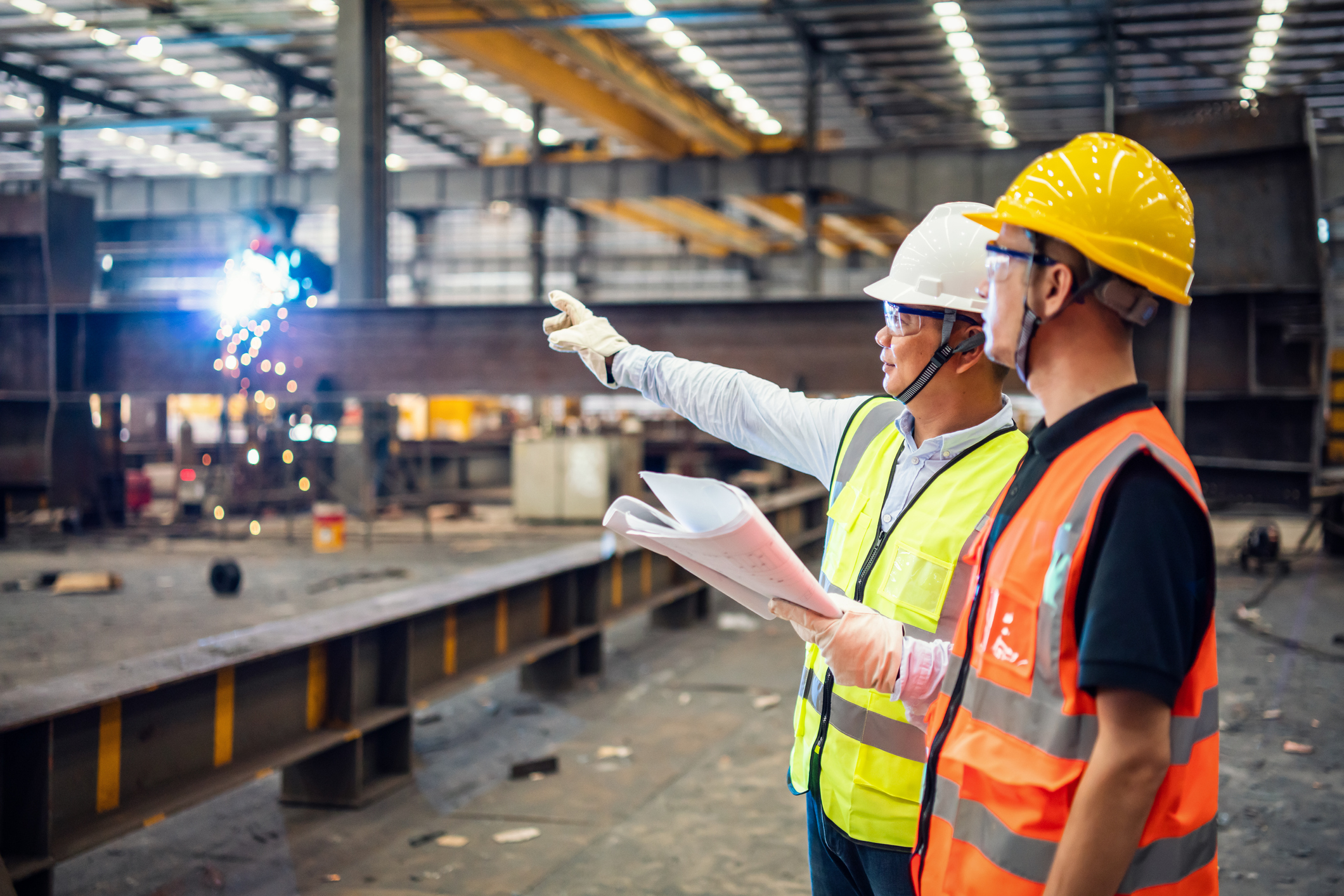
Ideal Practices for Quality Guarantee
Quality guarantee in welding is vital to accomplishing secure and long lasting building and constructions. Developing a comprehensive high quality administration system (QMS) customized to the certain welding task is crucial.
Regular Learn More training and certification of welding employees are important for maintaining a skilled labor force. Constant education on the most current welding strategies and innovations makes certain that inspectors and welders are educated about current standards and practices.
In addition, conducting pre-weld examinations to assess products and devices can protect against problems prior to they happen. Houston Welding Inspection. During the welding process, real-time surveillance and documents of welding specifications help determine inconsistencies promptly. Post-weld inspections must entail complete examinations utilizing non-destructive testing (NDT) approaches to ensure the stability of the welds
Furthermore, maintaining clear communication amongst staff member advertises a society of quality. Routine audits and evaluations of the welding procedure help determine locations for renovation. By sticking to these best methods, companies can attain optimum quality assurance, eventually bring about boosted safety and performance in metal construction jobs.
Obstacles in Welding Inspection
Although welding evaluation is critical for ensuring structural imp source integrity, it provides visit their website a range of difficulties that can complicate the evaluation process. One considerable difficulty is the irregularity in welding techniques and products utilized, which can impact the consistency of weld high quality. Various welders might utilize differing techniques, resulting in inconsistencies that inspectors requirement to identify and evaluate.
Another difficulty entails the discovery of issues. Non-destructive screening (NDT) approaches, such as radiographic and ultrasonic screening, can be intricate and need proficient professionals to translate results properly. False positives or downsides can happen, potentially leading to expensive rework or jeopardized safety.
Additionally, the visibility of environmental elements, such as temperature level and moisture, can influence the honesty of welds and the performance of inspection techniques. Examiners should likewise browse the regulative landscape, making certain compliance with industry criteria, which can vary by territory and application.
Final Thought
In conclusion, welding assessment plays a vital function in ensuring the honesty and safety and security of steel manufacture. Employing a variety of evaluation strategies, sticking to established industry requirements, and executing efficient high quality administration techniques collectively enhance the integrity of bonded structures. Despite the difficulties faced in the examination process, a dedication to continual enhancement and adherence to ideal practices can substantially bolster the high quality guarantee structure, promoting better confidence among stakeholders in the welding market.
Reliable welding inspection is necessary for recognizing defects that might endanger the top quality and sturdiness of bonded joints.In addition, consistent welding evaluations foster self-confidence amongst stakeholders, consisting of designers, clients, and regulatory bodies, by demonstrating a commitment to high quality guarantee.The American Welding Culture (AWS) and the American National Requirement Institute (ANSI) are 2 prominent organizations that establish welding standards. During the welding procedure, real-time monitoring and paperwork of welding parameters assist identify variances instantly. Regardless of the obstacles encountered in the examination procedure, a dedication to continual renovation and adherence to ideal techniques can dramatically strengthen the quality guarantee structure, fostering higher self-confidence among stakeholders in the welding sector.
Report this page